Semiconductor
Especially in the semiconductor industry, high-purity crystals have long played a vital role. As the basis for separating devices (e.g., transistors and diodes), microelectronics (e.g., memories and ICs), and microsystem components (e.g., sensors and converters), the purity of the crystal and its lattice structure must reach the highest standards.
We provide the following products:
Wafer Inspection Equipment
TWS206 measures wafer BOW, Warpage, TTV, LTV and thickness in high accuracy.
The toolsets are available in both semi-auto and fully automatic version. Support
connections with MES system. System uses optical confocal sensors, supports
transparent and non-transparent wafers made of various materials, including SiC,
GaN, Si, Sapphire, Glass, GaAs. It can be used across different production stages,
from cutting, grinding to thinning and polishing processes.
- BOW
- WARP
- TTV/LTV
- Thickness
- Wafer Sorting
- Support 4″,6″,8″,12″ wafer size
LFM-SiC series are specially designed for SiC wafer crystalline defects inspection.
With build-in well designed fine optics, and industry proven algorithm, it automatically
scan the wafer and classify the crystalline defects including TSD,TED, BPD and MP. The
toolsets are available in both semi-auto and fully automatic version. Support connections
with MES system. It improves your wafer qualification productivity, and reduces your
manual work and error dramaticall.
Type I–For KOH etched Wafer EPD detection
- TED/ TSD/BPD mapping
- Support original defects review function
- User friend interface and easy to operate
- Support 4″,6″,8″ wafer size
Type II–For polished Wafer MPD detection
- MPD mapping
- Support original defects review function
- Generate stitched stress map
- User friend interface and easy to operate
- Support 4″,6″,8″ wafer size
Measuring geometry dimensions of bevel edge, flat edge
length, notch, wafer diameter. Multiple measurements in
One Click. The toolsets are available in both semi-auto and
fully automatic version. Support connections with MES system.
- Wafer diameter D
- Wafer thickness T
- Bevel edge profile X, Y, R, A
- Flat edge and notch profile
- User friend interface and easy to operate
- Support 4″,6″,8″ wafer size
StressMap is a Tabletop tool. It is easy to operate, and can capture
the stress map within seconds. It helps review the strain pattern within
the SiC wafer qualitatively in most simple way, and all images can be
automatically archived and managed through the system. The toolsets
are available in both semi-auto and fully automatic version. Support
connections with MES system.
- Capture the stress map within seconds(each wafer<10s)
- User friend interface and easy to operate
- Support 4″,6″,8″ wafer size
Crystal Growth Furnace
Czochralski Method
Technical data
1. Height total incl. foundation: approx. 11,500 mm
2. Footprint: approx. 15m²
3. Weight (Puller): approx. 12,000 kg
4. Crucible size: up to 32″
5. Crystal length: up to 2,500 mm
6. Crucible charge size: up to 450 kg
7. Vessel height: approx. 2,100 mm
8. Inner diam. receiving chamber: 450 mm
9. Receiving chamber length: up to 3500mm
Technical Parameters
Float Zone
Since the emergence of Float Zone technology in the late 1950s, Haldor Topsoe has been actively engaged in the research and production of Float Zone wafers. During the development process, many special equipments for Float Zone wafer production were developed. In 2004, the equipment division of Haldor Topsoe was acquired by the PVA TePla Group of Companies and is now merged into Crystal Growing Systems, CGS. Float Zone gets its name from its special growth method. Firstly, the high-density Poly Rod produced by a special process from the Siemens CVD furnace is fixed in the Float Zone crystal growth equipment, and then the Poly Rod is heated to the conductor state by indirect heating, and then the induction coil takes over the heating to make the Poly Rod partially Melt, and then prepare a single crystal seed crystal at the bottom.When the silicon soup touches the single crystal seed crystal, it will begin to crystallize. At the same time, the single crystal seed crystal will rotate downward so that there is enough space for the silicon soup. Condensed into a single crystal rod. The biggest difference between the Float Zone and the CZ method is that no crucible is needed in the process, and there is no graphite element in the thermal field, so the crystal oxygen content and carbon content can be minimized, and it is suitable for semiconductor high- power components.The biggest difference between the Float Zone and the CZ method is that no crucible is needed in the process, and there is no graphite element in the thermal field, so the crystal oxygen content and carbon content can be minimized, and it is suitable for semiconductor high-power components.The biggest difference between the Float Zone and the CZ method is that no crucible is needed in the process, and there is no graphite element in the thermal field, so the crystal oxygen content and carbon content can be minimized, and it is suitable for semiconductor high-power components.
FZ-30 and FZ-35 are the largest zone-melting crystal growth furnaces for PVA TePla at present. The ingot diameter can reach 8 inches and the height can reach 2000mm. Its design makes the center of gravity of the machine just in the melting zone. In order to prevent external vibration, FZ-30 and FZ-35 are also equipped with an automatic adjustment system and a protection system. In addition, the main reaction chamber can also be equipped with a gas doping device.
Technical data
1. Max. Crystal Pulling length: 2,700 mm
2. Maximum poly length: 2,000 mm
3. Crystal diameter: Up to 200 mm
4. Pulling speed: 0 – 30 mm/min
5. Rotation speed: 0 – 30 rpm
6. Size: 3,800 x 4,050 x 11,550mm
7. Footprint(total): 5,000 x 6,000 mm
8. Weight(total): approx. 14,000 Kg
SR 110 (Slim Rod Puller) is designed to produce silicon core rods in Siemens CVD reactors. The diameter of the rods is about 7-10mm, and the height can reach up to 2.5 meters.
The SR 110 is a very efficient model because it can produce two silicon core rods at the same time in one manufacturing process. Compared with the CZ method and cutting with a band saw or wire saw, it can avoid material loss. In addition, the machine is designed after thorough consideration, so it is very easy to use, and after the production of a set of silicon core rods, the next set can be produced immediately. This is due to the special valves in the reaction chamber and the upper receiving chamber. design. Depending on the diameter of the raw material rod and the length of the required silicon core rod, one raw material rod can produce 12 to 50 silicon core rods.
Technical Data
1. The diameter of source rod: 25-50 mm
2. The length of source rod: max. 1000 mm
3. The quantity of source rod: 2
4. The diameter of slim rod: 7-10 mm
5. The deviation of the slim rod diameter: ±0.1 mm
6. The length of slim rod: max. 2500 mm
7. The quantity of slim rod: 2 (at the same time)
FZ-14M was born for testing needs. The principle of operation is to use the zone melting method to convert miniature polycrystalline silicon rods into single crystal silicon, and then put them into appropriate instruments to evaluate the quality and purity of the polycrystalline silicon materials. During the zone melting process, the polycrystalline rod is placed in an argon-filled environment to form a single crystal rod.
This single crystal rod will be analyzed by spectroscopic analysis for trace impurities such as boron, phosphorus, aluminum, arsenic, carbon and so on.
Features
1. No oil (hydrocarbons) at any component
2. Ultra low (no) natural pollution
3. Ultimate component quality
4. Low weight (aluminum frame)
5. Very suitable for polysilicon analysis
Vertical Gradient Freeze
VGF Kronos is a high-end VGF (Vertical Gradient Freezing) system for mass production of low-dislocation compound semiconductors with a diameter of less than 6 inches. The working pressure ranges from 10-3 mbar to 40 bar, and the replaceable core module provides a high degree of application flexibility.
Technical Data
1. Crucible Ø: up to 4″/6″
2. Max. Cylindrical length of crucible: up to 450 mm
3. Typ. Crystal length: up to 350 mm
4. Chamber Ø: 800 mm
5. Chamber height: 975 mm
6. Working pressure: max. 40 bar
Please contact us , we will contact you as soon as possible to discuss detailed specifications.
Quartz Crucible
Quartz Crucible
Quartz exists in the form of compound on the earth and is the second highet content of mineral only to feldspar, such as Silica, Silicate and so on.
Quartz, which is Silica, has the lowest coefficient of thermal expansion, high temperature resistance, high wear resistance, excellent chemical stability, electrical insulation, visible light penetration in ultraviolet(UV) and infrared(IR), high mechanical properties, etc.
Therefore, high-purity quartz materials are widely used in electronic technology, semiconductors, communications, electricity, light, solar energy, national defense, high-precision measuring instruments, laboratory physical and chemical equipment, nuclear energy, Nano-industry, etc.
* We can customize the specification.
Products Category
Material Purity
If you need further information, please contact us, we are happy to discuss with you !!
Automatic Equipment
Grinding Machine
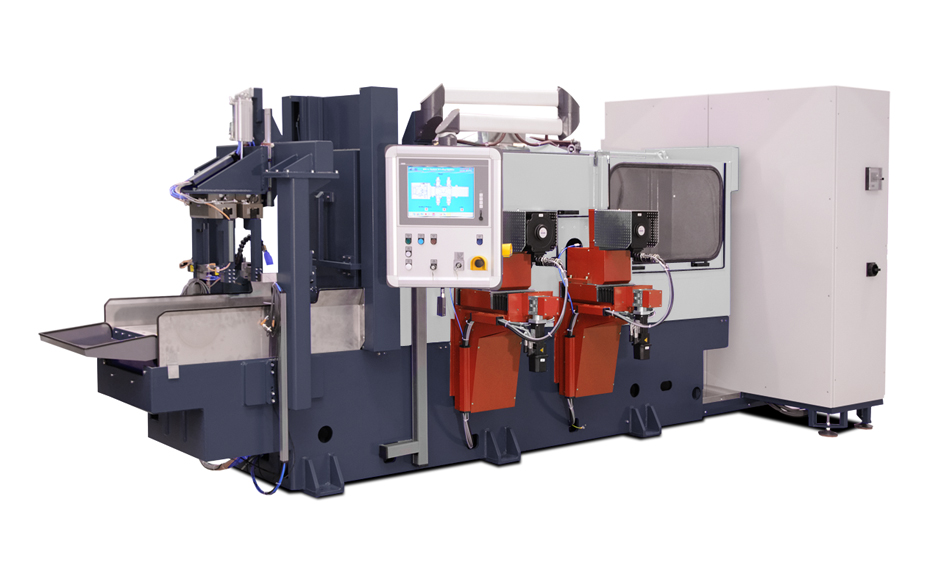
The surface grinding machine uses two parallel grinding spindles for processing. The machine design can be loaded manually or by the arm for grinding and loading and fully automated integration with analysis system. The machine can handle silicon bricks with a size range of 125mm x 125mm to 156mm x 156mm and a length of 180mm to 1000mm.
Features |
1. The grinding size can be automatically switched (125/156) |
2. Equipped with a manual loading area and a fully automatic loading area |
3. Equipped with pneumatic silicon brick fixture |
4. The monocrystalline silicon ingots and polycrystalline silicon bricks after the square can be polished without first cutting the head and tail. |
5. Automatic compensation and correction system for diamond layer consumption of grinding disc |
6. Detect and evaluate the quality data of working parts immediately after grinding |
7. Machine capacity: equivalent to 40,000 bricks/year (when the machine capacity is fully opened and uninterrupted; the processing size of silicon bricks is 156x156x350 mm) |
8. Grinding time: each silicon brick is ground for about 10min/350mm |
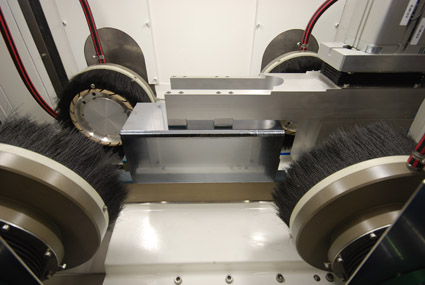
model | 72/860.500- 125/156 | 72/860.1000- 125/156 |
Working part length | 180mm-500mm | 400mm-1000m |
The chamfer grinding machine is suitable for the chamfer grinding of the single-poly crystals that have been squared and the surface is ground. The size of the silicon bricks is 125 x 125 mm and 156 x 156 mm. The machine is equipped with a pair of parallel grinding tool sets. Working parts with a length between 180 and 500mm can be processed directly.
Features |
1. 45 ° angle chamfer grinding |
2. Equipped with a manual loading area and a fully automatic loading area |
3. Equipped with pneumatic clamp |
4. Automatic edge detection and grinding tool correction |
5. Automatic compensation and correction system for diamond layer consumption of grinding disc |
6. Detect and evaluate the quality data of working parts immediately after grinding |
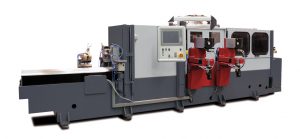
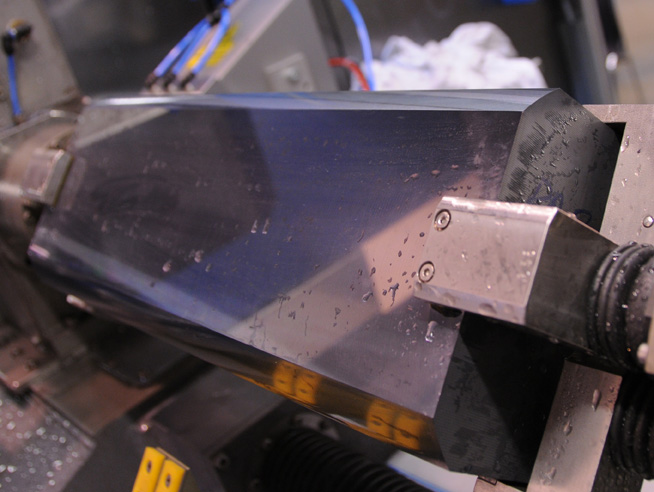
Features |
1. It can grind 45° degree chamfer to round chamfer |
2. Equipped with pneumatic silicon brick fixture |
3. Automatic edge detection and grinding tool correction |
4. Detect and evaluate the quality data of working parts immediately after grinding |
5. Automatic correction system for diamond layer of cutting disc |
6. Equipped with a manual loading area and a fully automatic loading area |
model | 72/856.600 -156/210 | 72/856.600 -125/156 | 72/856.1000 -156/210 | 72/856.1000 -125/156 |
Silica brick size | 156 mm x 156mm 210 mm x 210 mm | 125mm x 125mm 156mm x 156mm | 156 mm x 156mm 210 mm x 210 mm | 125mm x 125mm 156mm x 156mm |
Working part length | 180mm-600mm | 180mm-600mm | 450mm-1000mm | 450mm-1000mm |

Features |
1. The grinding size can be switched according to product requirements (125/156) |
2. Different modes can be switched according to product requirements (surface grinding + chamfering, simple surface grinding, simple chamfering processing) |
3. Equipped with a manual loading area and a fully automatic loading area |
4. Equipped with pneumatic silicon brick fixture |
5. The monocrystalline silicon ingots and polycrystalline silicon bricks after the square can be polished without first cutting the head and tail. |
6. Automatic compensation and correction system for diamond layer consumption of grinding disc |
7. Detect and evaluate the quality data of working parts immediately after grinding |
8. Machine capacity: equivalent to 31,000 bricks/year (when the machine capacity is fully opened and uninterrupted; the processing size of silicon bricks is 156x156x350 mm) |
9. Grinding time: each silicon brick is ground for about 14min/350mm |
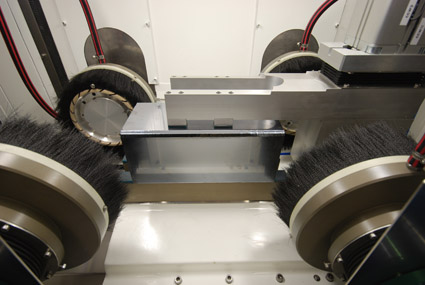
model | 72/860.500- 125/156 | 72/860.1000- 125/156 |
Working part length | 180mm-500mm | 400mm-1000m |
This machine is suitable for grinding silicon carbide ingots with 4″-12″ chamfers. The length is 600 mm, with straight notches and flat grinding. The centering of the parts is done automatically.
Ingot size:
-Diameter: 4-12 inches
-Length: 30mm-600mm
Freiberg Instruments’ XRD orientation measurement
- Online inspection 4″-12″
- Crystal orientation (111), (100), (110)
- Flat edge/groove position measurement
- The depth or width of the flat edge/groove
- Diameter measurement of bare rods and round grinding rods
Grooved grinding wheel:
1-2 different types of grinding wheels
Groove rough and fine grinding
Loading station:
Automatic loading and unloading
Scan the ingot identification code
Cutting Machine
72/360 This machine is suitable for cutting squared multi and mono crystalline silicon work pieces. Also, it is used for Top and Tail cutting, recycling cuts and analysis wafer cutting. The suitable workpiece length is from 50 to 550 mm and the suitable diameter is from 120mm to 160mm. the analysis wafer thickness is less than 1.5 mm.
To suit the needs of the customers, the machines can be equipped with the specially developed software ARPAT for the acquisition and analysis of your production information. These can be stored in a Microsoft SQL-database and can easily be supervised worldwide from your own computer.
Advantages |
1. Equipped for manual and fully automatic loading |
2. Low kerf-loss by thin blade guidance ≤ 1,7 mm |
3. Low kerf loss: less than 1.3mm |
4. Over 6 months of high wheel lifetime |
5. Machine capacity: approx. 52.000 cuts/year(based 24 hour mass-production) |
The machine is suitable for cutting mono crystalline silicon work pieces length is 1200 to 3000 mm. and work piece diameter up to 230 mm, the each brick length is 200 to 1020 mm.
Advantages |
1. Fully automatic load and unload, fixed position, top and tail cutting and analysis wafer cutting. |
2. Use the thin film blade and low kerf loss is less than 1.3 mm |
3. Longer band saw life time (approx. 12000 to 15000 cuts) |
4. Processing of different brick or ingot sizes (125 x 125, 156 x 156, 210 x 210 mm) |
5. Lower tool costs |
This machine is suitable for cutting single crystalline and multi crystalline silicon work pieces up to diameter format of max. 210 x 210 mm with a work piece length between 100 and 500 mm. Minimum segment length is 10 mm.
Advantages |
1. Pneumatic clamping of work piece and segment |
2. Equipped for fully automatic or manual loading |
3. Low kerf loss: less than 1.3mm |
4. Processing of different brick or ingot sizes (125 x 125, 156 x 156, 210 x 210 mm) |
5. Quick set-up time |
6. Longer band saw life time ( depend on brick and ingot size 156 x 156 approx. 850 cuts; 125 x 125 approx. 1300 cuts) |
7. low tool costs |
For cutting from monocrystalline Ingot´s up to a Ø 320 mm
Advantages |
1. Test wafer thickness: 1 – 3 mm |
2. Length cylindrical part: 3500 mm (in depends on the customer specification) |
3. Single cuts possible; Diameter: 4 – 12“ ; Top/Tail cropping |
4. Infeed accuracy of the X-axis block and disc infeed < 0.01 mm |
5. latness (Bow, Warp, Shape, Linear Shape Range) <= 70 μm |
6. Squarness of the test discs: < 0,1 mm ; Cutting force (pressure sensor monitoring) limit value: adjustable |
7. Belt tension limit value: ± 1.5 ; Belt speed limit value: ± 2% |
Argon Recycling System
In order to save huge amount of argon when producing mono ingots, ReiCat develops and produces systems for the most efficient application of valuable technical gases. Our customers will no longer need to spend lots of money buying argon.
Advantages
1. Reduction of argon consumption of more than 80%
2. Fully automatic operation with remote control
3. Short amortization period
4. Guaranteed gas quality higher than 99.999%
5. Active and sustainable environment protection
6. 3 different process capabilities: 100m3/hr, 200m3/hr, 400m3/hr
7. Other technical gases recycling system is also available
Sensors
In our proprietary glass blowing and mechanical engineering department, we manufacture a wide range of sensors for the measurement of pH value, redox potential, conductivity and temperature. Our sensors are available in glass and plastic design. With great technical skills, each individual sensor will be manually manufactured by us. Besides proven standard products, we offer custom-made products to your exact specifications. For best results, the construction and the selection of materials are made in close cooperation with our customer.
Special sensor cables, special plug and screw-type connections, fixtures and level indicators of different types as well as other accessories round off our wide range of modern sensors.
For more details, please contact us. We are willing to help!
Actuators, Valves and Accessories
The diversity of process technology and the thereby processed mediums is reflected in an even larger diversity of products which are deployed in plant construction.
The arrangement of products presented here is only a small representative selection from our total range of products. This range of products includes pneumatic and electric actuators, positioners, limit switch boxes, pressure boosters or reducers as well as solenoid valves.
All products are available in groups or as singles, fitted out with manual or automatic valves or even in special combinations whereby the perfect solution will be found for each and every actuator interface.
We can provide our customers with consultation and layout suggestions. In addition, we can provide training for the employees as well as supporting services according to your demand.
Please find out a brief introduction below of our products:
Valves
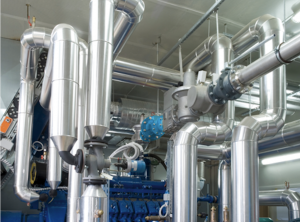
Actuators
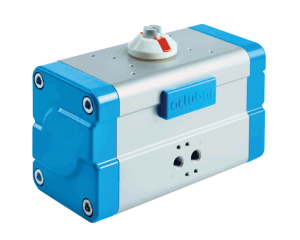
Electric actuator
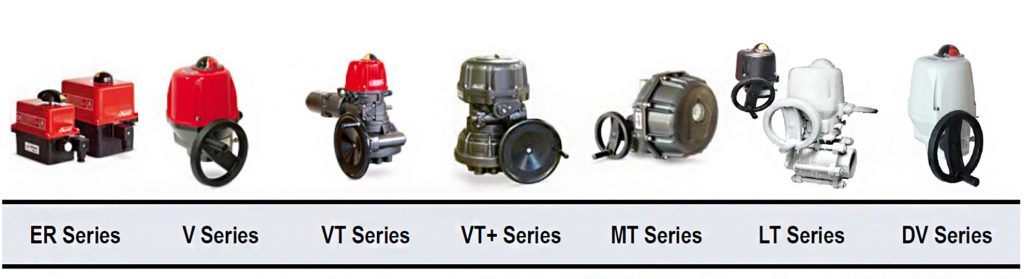
The electric actuator series have a wider range of services, and can be equipped with PLC, Internet, Bluetooth, Wi-Fi, etc., and can support mobile phone or tablet.
Besides, the DV series has been certified by DNV GL, and is suitable for ships, offshore units and light craft. In 2020, it won the French navy tug supply contract.
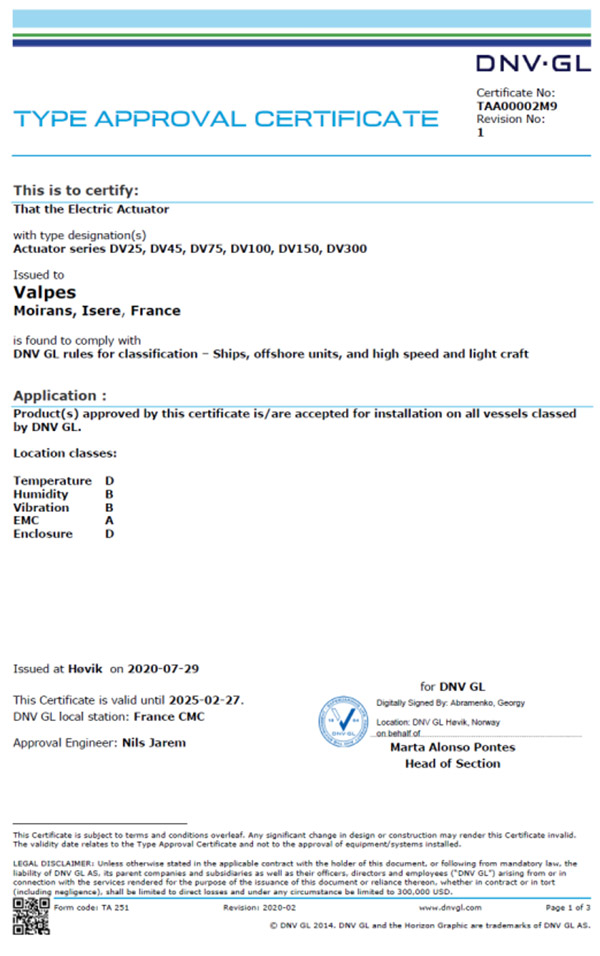
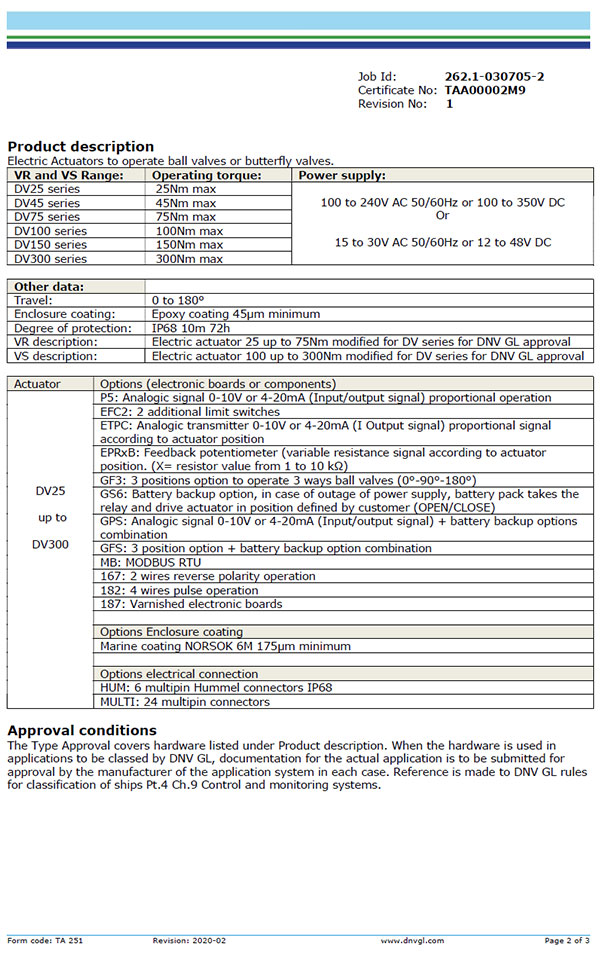
Accessories
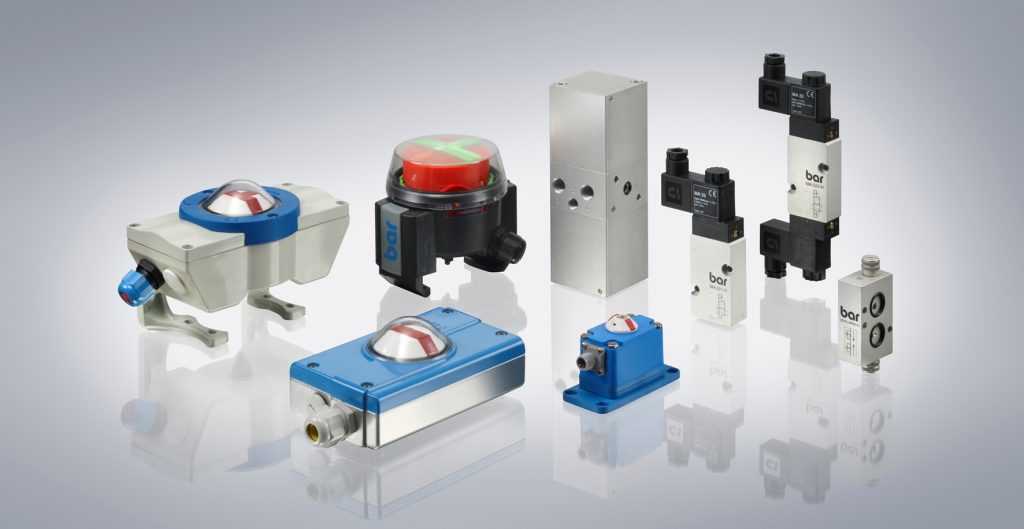
Sawing Wire
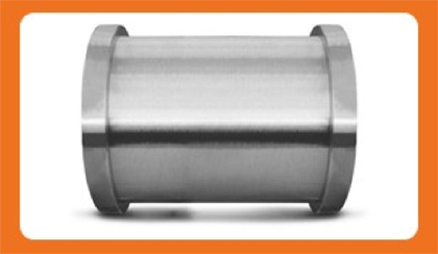
Product Advantages
1. Less kerf loss
2. Higher efficiency, capacity and precision
3. Lower processing cost
Diamond Wire is a special high strength steel wire with single layer diamond abrasives fixed on its surface. According to the diamond bonding process, it can be divided into Resin bonded diamond Wire(RW),the Electroplated diamond Wire(EW) and Diamond Cable( DC).It has strong cutting capability for sawing large size, super hard and brittle crystalline materials, such as monocrystalline/polycrystalline silicon ,silicon carbide, sapphire, crystal and other precious crystals. Compared with free abrasive sawing wire. The advantages of diamond wire is lower overall processing costs, improvement of processing quality and reduction of environmental influence etc.
Product Advantages
1. Shorter cutting time, better total thickness variation
2. Slurry-Free and environment-friendly process
3. Reducing the total cost of ownership