Industrial furnace
PVA TePla is an expert in vacuum equipment, with more than 20 years of experience. We have rich experience in high temperature and high pressure furnaces. Our customers are all over the world, and some models account for more than 50% of the global market. We can produce high-temperature furnaces with the highest quality and high safety. The maximum operating temperature can reach 3000 degrees Celsius. We build the gas environment specified by the customer, whether it is chlorine, argon, silyl methane, nitrogen, etc.
We can do:
- High temperature below 3000 degrees Celsius
- Air pressure 200 bar or vacuum environment
- Various gas combinations
- Fast heat dissipation device
- Precise temperature control
- Graphite heating rod or molybdenum metal heating rod
We provide the following products:
Sinter HIP Furnaces COD
COD’s vessels are double-walled for water cooling, made of fine grain steel, in a horizontal and vertical design. The heating insert is made of graphite. Due to separately controlled heating zones, gas pre-heating, the most efficient design of thermal insulation, extremely accurate measuring and control system, an optimum temperature homogeneity can be achieved in the useable space. Compared to conventional designs, the special design of the thermal insulation results in a considerably extended lifetime and reduced heat losses.
A microprocessor controlled program sequence ensures a fully automatic and reproducible process and uniform product quality. PC-operating and related data handling comply with the demand for responsible quality assurance.
Application:
A. Dewaxing
1. of green bodies manufactured with methods like form pressing, extruding or PIM-technique |
2. with partial pressure (Ar, N-2, H-2) |
3. with pressure control and monitoring of binder evaporation |
4. for all conventional binders: conventional paraffines, PEG, micro wax, methyl cellulose etc. |
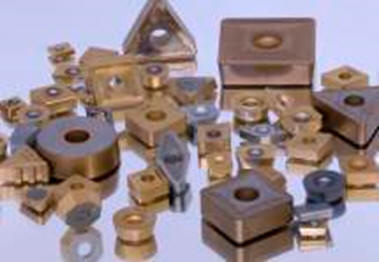
1. for isostatic compaction with inert gas at sinter temperature (HIP) |
2. process under high pressure or vacuum/td> |
3. high pressure rapid cooling from sinter temperature with cooling fan/td> |
C. Material
1. Hard metals |
2. PM-special alloys |
3. Technical ceramics |
Design Versions:
Type: COD 733 RL![]() |
Operating pressure: 60/100 bar |
Usable space (WxHxL): 500x550x3000 /500x475x3000 mm |
Usable volume: 825/712 L |
Charge load: 2,500 kg |
Power rating: 700/760 kVA |
Type: COD 733 R![]() |
Operating pressure: 60/100 bar |
Usable space (WxHxL): 500x550x1600 /500x475x1600 mm |
Usable volume: 440/380L |
Charge load: 1,500 kg |
Power rating: 465/525 kVA |
Type: COD 663 R![]() |
Operating pressure: 60/100 bar |
Usable space (WxHxL): 500x550x1000 /500x475x1000 mm |
Usable volume: 275/240 L |
Charge load: 1,000 kg |
Power rating: 335/415 kVA/td> |
Type: COD 533 R![]() |
Operating pressure: 60/100 bar |
Usable space (WxHxL): 300x300x900 /300x260x900 mm |
Usable volume: 81/70 L |
Charge load: 300 kg |
Power rating: 190/210 kVA |
Type: COD 033 RL![]() |
Operating pressure: 100 bar |
Usable space (WxHxL): 150x100x300 mm/td> |
Usable volume: 4.5 L/td> |
Charge load: 30 kg/td> |
Power rating: 50 kVA/td> |
Type: SSH/SSH+ (SSH+ with dewaxing unit)![]() |
Operating pressure: 60 bar |
Usable space (WxHxL): 500x540x1500 mm |
Usable volume: 405 L |
Charge load: 1,200 kg |
Power rating: 400 kVA |
* Note: SSH/SSH+is a standard type of COD system with attractive price segment but without customized adjustments. |
Vacuum - Heat Treatment and Sintering Furnaces COV
COV furnaces are graphite-heated systems which are designed for heat treatment in vacuum. The design of usable space, vacuum level, and working temperature are various. As a consequence, COV furnaces can be used for numerous applications. Typical applications are sintering (including dewaxing), soldering, degassing, heat treatment, purification, CVD-coating, etc.
A COV furnace contains a double-walled vessel which is water-cooled. The vessel can be made of mild steel or stainless steel respectively, depending upon the process requirements. The general design can be horizontal or vertical. The number of controlled heating zones can be up to 8 (or even more). By adjusting the number and the arrangement of these control zones, an excellent temperature homogeneity can be achieved; however, in some cases, it can be better than ± 2°C.
COV furnaces have very low “Total Costs of Ownership“ due to high reliability, process reproducibility and a long lifetime. The system is proper for cleaning graphite materials such as MOCVD trays or hot zones, in LED, semiconductor and solar industries.
Application:
- 1,100 °C – Heat treatment, soldering, degassing, dewaxing, chemical reduction
- 1,350 °C – Heat treatment, soldering, degassing, dewaxing, sintering, CVD-coating
- 1,600 °C – Dewaxing and sintering of hard metals, crystal growth, purification, CVD-coating
- 1,800 °C – Sintering of non-oxide ceramics
- 2,000 °C – Pyrolyze processes, degassing and purification, sintering
- 2,200 °C – Degassing, purification, sintering of SiC, graphitizing of composites
Features:
1. Maxium working temperature 2200℃
2. working space:4.5 ~ 2250 L
3. The number of controlled hot zones can be up to 8, according to requirements of customers
4. Excellent temperature homogeneity within the usable space, ±3°C
5. Vacuum range down to 1 x10-5 mbar
6. Efficient dewaxing systems for molded and extruded parts
7. Can process under flammable gases
8. Operation of the plant by PC including data logging and data storage
9. design can be horizontal or vertical
Design Versions:
Type: COV 1263 R![]() |
Operation temperature: 2,200 °C |
Usable space (WxHxL): 1400 x 800 x 2000 mm |
Usable volume: 2,240 L |
power rating: 800 kVA |
Type: COV 942 R![]() |
Operation temperature: 1,800 °C |
Usable space (WxHxL): Ø 1500 x 2500 mm |
Usable volume: approox. 4,400L |
power rating: 500 kVA |
Type: COV 633 R![]() |
Operation temperature: 1,600 °C |
Usable space (WxHxL): 450 x 450 x 900 mm |
Usable volume: approx. 182 L |
Power rating: 120 kVA |
Type: COV 231 R![]() |
Operation temperature: 1,600 °C |
Usable space (WxHxL): Ø 200 x 300 mm |
Usable volume: approx. 9.4 L |
Power rating: 25 kVA |
Type: COV 131 R![]() |
Operation temperature: 1,600 °C |
Usable space (WxHxL): Ø 150 x 250 mm |
Usable volume: about 4.4 L |
Power rating: 20 kVA |
Type: COV 733 R![]() |
Operation temperature: 1,700 °C |
Usable space (WxHxL): 1,000 x 500 x 750 m |
Usable volume: approx. 375 L |
Filler amount: up to 600 Kg |
Temperature range: ± 10K |
Induction Heated Vacuum Heat Treatment Systems IOV
Induction heated vacuum furnaces (IOV) are rugged vacuum systems which are designed to handle particular high temperature processes. Each furnace can be operated up to 1600°C or 2200°C. PVA adopt the IOV system’s heating device, which contain a 2~4kHZ medium frequency power supply, a set of heating coils and a set of graphite bases, which has a layer of graphite felt to isolate thermal energy.
Application:
Sintering processes
Degassing
Graphitizing/span>
Carburization;
Reducing
Distillation
Impregnation
Features:
The highest working temperature: 2200℃ (It can be customized to the higher temperature.)
usable space: 34 ~ 338 L
Temperature uniformity reach ±10°C in the working area
Applicable pressure range: 10-3 ~ 1050 mbar
The vessel is vertical
Resistance Heated High Vacuum Heat Treatment Furnace MOV
MOV systems are cold-wall furnaces with water-cooled double wall vessels of stainless steel. The material to be treated is heated by full metal resistance heater. Here the heat transfer takes place directly via heat radiation from the heater to the thermal treatment product. Thermal insulation is provided by metal sheets and multi layer foils. The all-metal design of the MOV systems is particularly well suited for high vacuum operations. Due to its high vacuum conduction, short pumping times and low ultimate vacuum pressure are ensured. Appropriate accessory equipment also allows operation under partial pressure or overpressure protective or process gas atmosphere.
The MOV-HP system is basically the same like MOV. but it had additional pressing unit. The installation of pressing plates and punch can be effected both metallically and with graphite. Thermal insulation is provided by metal sheets and multi layer foils. This pressing unit allows more application like diffusion bonding to process in the system. The force provide from the pressing unit could be up to 2500 N.
Application:
Bright and stress-free annealing
Degassing and cleaning
Sintering processes
Annealing processes
Vacuum and protective gas brazing
Hot press process like diffusion bonding
Feature:
Usable volume: 0.1~1200L
Design can be horizontal or vertical
Heater material can be choce from Stainless steel, molybdenum, tantalum and tungsten, temperature could be up to 2400°C
Temperature homogeneity in usable space ±5°C
Ultimate vacuum: 1 x10-6 mbar
Leakage lower than 1 x10-4 mbar
High thermal efficiency, low energy consumption
Operation of the plant by PC including data logging and data storage
Material:
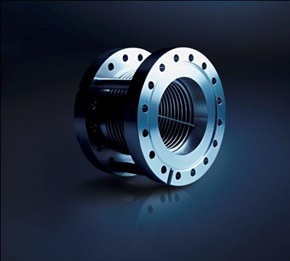
1 Stainless steel
2. Refractory metals
3. Precious metal alloys
4. Superalloy
Design Versions:
Type: Laboratory Furnace
![]() |
Ultimate vacuum: 10-6 mbar |
Usable volume: 0.1~0.66 L |
Operation temperature: 1100~2500 °C |
Type: Horizontal
![]() |
Ultimate vacuum: 10-6 mbar |
Usable volume: 8~1200 L |
Operation temperature: 1350 °C |
Type: Vertical (Top Loader)
![]() |
Ultimate vacuum: 10-6 mbar |
Usable volume: 4.4~10 L |
Operation temperature: 1350 °C |
Type: Vertical (Bottom Loader)
![]() |
Ultimate vacuum: 10-6 mbar |
Usable volume: 150~600 L/td> |
Operation temperature: 1350 °C/td> |
Type: MOP-HP
![]() |
Take-up path precision: ≦ 0.1mm |
Ultimate vacuum: 10-6 mbar |
Maximum force: 2,500 kN |
Operation temperature:1400 °C (with pressing unit 1200 °C) |
Vacuum Induction Melting and Casting Systems VSG
The VSG systems can be universally employed for melting of metals, alloys or special materials in crucibles made of ceramics or graphite under high vacuum, fine vacuum or different gas atmospheres with subsequent casting into moulds or forms in laboratory or production
VSG systems are cold-wall furnaces of corrosion-resistant stainless steel with water-cooled double wall vessel. The melting and casting device consists of a tiltable induction coil with coaxial power and coolant feedthrough and the mould table. The material of the applied crucibles is adapted to the melting material. If the melting material is non-reactive with carbon, crucibles made of graphite or clay-graphite can be used. Otherwise ceramic crucibles will be used. Where required crucibles of high-melting metals may also be employed as far as the melting material does not react with the crucible material. In these cases, the crucible acts as a secondary winding for power induction. Power is supplied by static medium frequency converter systems.
VSG systems are available as single or multi chamber systems and consist of the following basic modules: furnace vessel, vacuum pumping unit, power supply and control system, melting and casting equipment, as well as vacuum-lock for melt manipulations. These modules are to be supplemented according to need in different versions combinable and by an extensive selection of accessory mechanisms.
Material:
1. Precious metals
2. Highly pure, highly alloyed steel
3. High temperature resistant materials on Fe-, Ni-, Co- basis
4. Superalloy
5. Non-ferrous metals
6. Solar silicone and special materials
Feature:
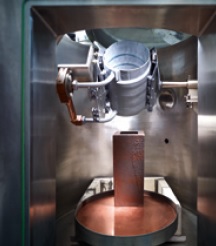
1. Working temperature can be up to 2200℃,(can be higher in customized adjustments)
2. Usable volume: 0.1 ~ 60 L
3. temperature homogenious in work space ±10°C
4. pressure range from 10-3 to 1080 mbar
5. Automatic control of the melting and casting process
6. Tilting of crucible under full power load
7. Suitable for ingot-, mould- or precision-casting
8. Well structured systems with a high application flexibility, suitable for modular extension or later supplement / conversion
* Please contact us for more product details.
Diffusion bonding furnace(MOV-HP)
Diffusion bonding is a connection process of material bonding. It is carried out by applying pressure under high vacuum and high temperature. The material is first heated to the required temperature, and the pressure is matched, and the bonding surfaces of the material begin to contact closely, resulting in diffusion phenomenon and crystal grain growth. , So that the seam is completely connected, and there is no connection line in the middle, and the process does not use flux or any auxiliary bonding material./span>
For example, stainless steel, tool steel, aluminum, nickel super alloys, ceramics, glass, copper, as well as composites such as steel-copper, titanium ceramics and titanium steel or sensitive materials such as titanium, niobium and zirconium, etc., can be used for diffusion bonding
Diffusion bonding has a wide range of applications, such as the bonding of homogeneous and dissimilar materials, aluminum bonding in the aerospace industry, mold industry, heat exchangers, semiconductors, etc., all of which are applicable.
Advantages:
1. No flux or other substances in the process
2. No liquid phase during the entire connection
3. High vacuum environment, sensitive materials (Ti, Nb, Zr) can also be welded
4. Very high strength, close to the strength of the base material
5. Corrosion resistance
6. The connection line is not visible visually
7. Composite materials of similar materials such as stainless steel, tool steel (1.2083, M333, etc.), titanium, aluminum, nickel super alloys, ceramics, glass, copper, etc.
8. Composite materials of different materials can be used: steel-copper, titanium ceramic, titanium steel, etc.
9. Large area composite material, no deformation
Features:
1. Pressure plate accuracy: ≤ 0.1mm Ultimate vacuum: 10-6 mbar ; Maximum force: 2,500 kN
2. Maximum working temperature: 1400 °C (the pressure plate can work at 1200 °C)
3. In the working area, the temperature uniformity reaches ±5°C
4. Ultimate vacuum 1 x10-6 mbar
5. Leak rate is less than 1 x10-4 mbar
6. Low energy loss, high heat utilization rate
7. All data are stored in the computer and presented with a humanized interface
* Please contact us for more product details.Graphite Purification Furnace
Graphite materials can be used in a variety of industrial applications, such as parts of crystal growth furnaces, insulating materials at extremely high temperatures, current carrier systems, etc. Because of their high heat resistance and chemical resistance, it has a wide range of applications in the fields of chemical industry, chemical industry and nuclear engineering.
In order to be able to use graphite in higher purity application environments, such as semiconductor production, graphite must have higher purity. When heated to a temperature of up to 2400°C under near vacuum or low pressure, many elements (especially metal elements) will form very stable carbides. With the help of chlorine and fluorine, chemical reactions can be harmlessly performed in the furnace and the graphite can be purified.
Application of High Purity Graphite:
Graphite heating element for vacuum furnace and crystal growth system
Insulating graphite felt in vacuum furnace and crystal growth
For epitaxy and coating
COV graphite purification furnace is suitable for cleaning graphite materials and impurities in MOCVD trays. It is suitable for LED, semiconductor, solar and other crystal growth industries that have certain requirements on the purity of materials.
Application:
- 1,100 °C heat treatment, welding, degassing, dewaxing, reduction reaction
- 1,350 °C heat treatment, welding, degassing, dewaxing, sintering, CVD coating
- 1,600 °C dewaxing, hard metal sintering, crystal growth, purification, CVD coating
- 1,800 °C oxygen-free ceramic firing
- 2,000 °C thermal cracking, degassing, purification, sintering
- 2,200 °C degassing, purification, silicon carbide sintering, graphitization
Features:
1. The maximum working temperature is 2200℃
2. Available space: 4.5-2250 L
3. According to customer needs, different numbers of independent heating can be configured (up to 8)
4. In the working area, the temperature uniformity reaches ±3°C
5. Ultimate vacuum 1 x10-5 mbar
6. Efficient dewaxing for die casting, powder metallurgy and other workpieces
7. Able to process under flammable gas
8. All data are stored in the computer and presented with a humanized interface
9. Choose vertical or horizontal furnace
* Please contact us for more product details.
SNOL Furnace
High temperature Muffle furnaces
Fast heating time
Low power consumption
Good stability ± 1°C
Thermal shock resistant
Uniformity ± 10 °C
Temperature measured in 9 points
APPLICATION: METAL, GLASS
PROCESS: SINTERING TEMPERING SOLDERING BRAZING FUSING
Low temperature Chamber Ovens 300 °C
OTP and buzzer
Fan speed controller
Uniformity ± 1 – ±5 °C
Temperature measured in 9 points
PROCESS: DRYING
SNOL Industrial Applications
Conveyor Oven Designed for Drying Wet Parts
Adjustable heating time
Adjustable speed of belt
Heating zone length: 2m
Handling zone at the entrance and exit: 1,5m
1 operating person
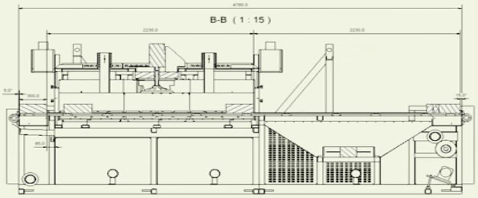
Oven for Audi’s Experimental Work
Double doors
Stainless steel chamber
Short heat up time
Air circulation
Air intake and exhaust vents
Adjustable automatic valves
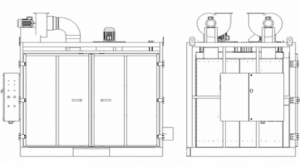
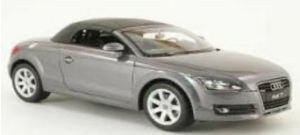